Selecting the right sensors for predictive maintenance can be a jungle. This blog post will give you advices for what to look for and how you can get started on your journey. We will also take a look into common pitfalls and what you need to be aware of as a customer to get the right sensors which fits your production.
Predictive Maintenance
Predictive Maintenance at its core tries for find the optimum between using components to their fullest but ensure that a repair happens before there is a breakdown. To find this optimum we need to use sensors to monitor an asset and its components to ensure that we find this optimum which can both reduce costs and ensure a high uptime. An asset could be a bearing, and components are in general all rotating parts, e.g. pumps.
If you want to know more about if it is worth reducing unplanned downtime with predictive maintenance you should read this previous blog post.
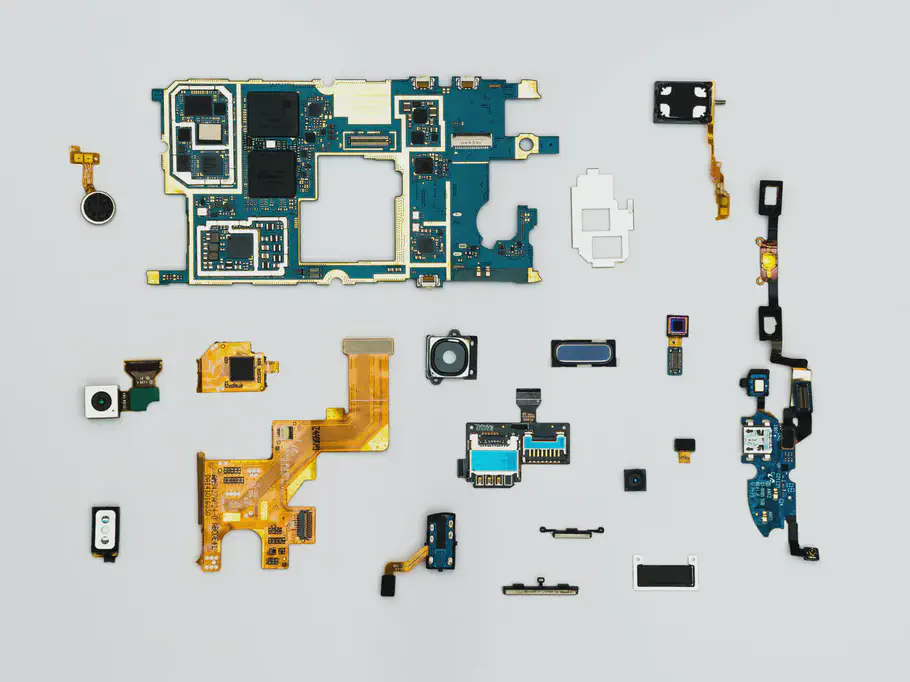
Different sensors and components from a mobile phone
One of the first questions that arise when starting on the predictive maintenance journey is what sensors should you choose? What is important to look for when you want sensors for predictive maintenance? Together we will go through the most important aspects to look for but first we need to talk about the P-F interval.
P-F interval and which sensor to choose
As we have previously blogged about The P-F interval and Predictive Maintenance, the P-F interval describes the time between signs of a potential failure is spotted, and when the functional failure occurs. An example is from when we see smoke until the asset breaks down. As you likely know this period is rather short but what about temperature versus vibrations? Is one type of measurement better than the other when trying to monitor for potential failure as early as possible?
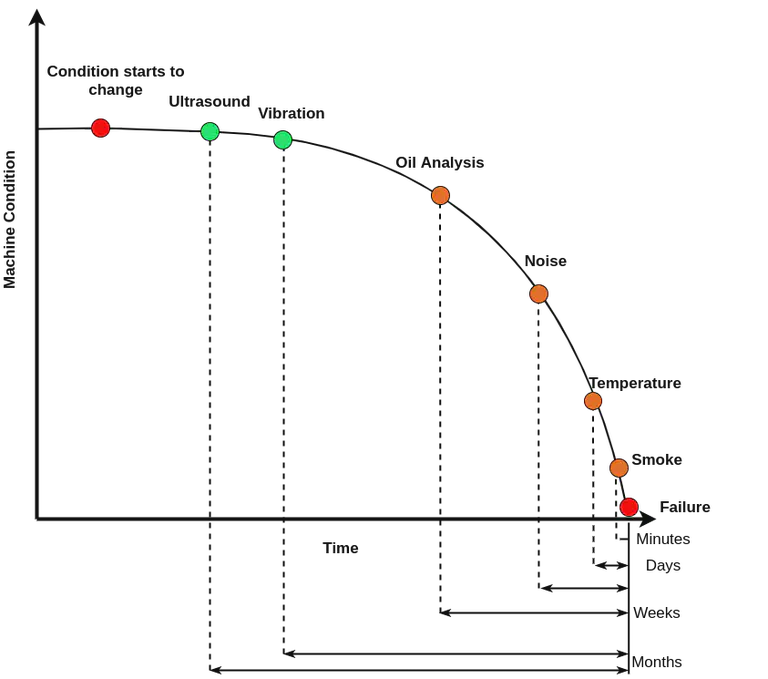
P-F Interval for different sensors
As you can see from the diagram above smoke and higher temperatures are the last symptoms which shows changes in a components condition before an initial breakdown. These can give you indications that the failure soon is going to happen. The interval is between minutes and a couple of days.
Noise is possible to detect before this and will be able to spot the failure days to weeks before a breakdown will occur. But this requires that highly skilled maintenance workers, who knows when their components have a normal, or abnormal sound.
Oil Analysis can detect problems weeks in advance and can be a good supplement to other types of sensors.
Vibrations and ultrasound sensors can detect the symptoms of a potential breakdown months in advance providing you with the longest time to react and the best P-F interval.
All of these results are based on research done by various parties both industrial and universities. We are currently doing research projects in neurospace to validate these findings, specifically how good predictions we can get with vibration and ultrasound sensors including the difference between them.
We encourage you to focus on Right Data over Big Data and select the types of sensors which is most likely to give you the result you want instead of just selecting all of them. Currently we are helping many of our customers with vibration sensor combined with machine learning for predictive maintenance and we want to share with you the most important characteristics for selecting the right vibration sensor for your rotating equipment.
Vibration sensors
Vibration sensors are widely available and comes in almost all forms and sizes you can think of. When we measure vibrations we actually use accelerometers which can say something about movement in one or more directions and vibrations are just movement.
Type
Vibration sensors comes in different types and you need to be aware of their differences. Piezoelectric depend on changes in electric current due to motion. They often have a very wide frequency response, a good sensitivity, have low noise levels, but can be expensive. Piezoelectric accelerometers have been build for many years and therefore there are many different models available for different applications. MEMS or micro-electro-mechanical systems are often small sensors which is often used in IoT deceives for detecting vibrations. These sensors are often cheaper than their Piezoelectric counter parts. You likely have one inside your smart phone which is used for various accelerometer tasks such as detecting motion. Both piezoelectric and MEMS accelerometers can be used to monitor low and high frequency vibrations.
Frequency Response
The frequency response of the sensors you choose is very important. You can see it as the specification of how much you can possibly see in terms of Hz in an vibration. For example if you have a sensor which can only detect 1 to 10Hz vibrations and the potential failure you are looking for is present at a 100Hz you will never see it. In general the higher frequency response on the sensor the better as this gives you more wiggle room to detect potential failures. Another rule of thumb is that vibrations due to degradation of a bearing will first be visible as high frequencies and then later move down to lower frequencies. If you can find sensors with a frequency response around 10 to ~8500Hz in x, y and 5000Hz in z these are good enough to do predictive maintenance. Are you looking for the best sensors on the market you can even get around 1.5Hz to 12kHz on 3-axises.
Axises
An accelerometer can measure vibration in up to three axises, often referred to as the X, Y, and Z axis. A vibration can be detected as movement from side-to-side, forward/backward, and up/down. To be able to see the full movement of the vibrations, we highly recommend you to buy a sensor 3-Axis as opposed to 1-Axis sensors. As the axises all detects part of the vibration and together they are strongly correlated making it easier to detect potential failures when having a 3-Axis sensor.
Sample Length & Interval
The last piece in the puzzle is sample length and interval. The interval defines how often does the sensor start and sample. The length defines for how long the sensor is sampling e.g. 1 second or 10 seconds? This has often to do with if the sensors are battery powered as this will be a constraint resource and therefore if you were to sample all the time the battery would likely die in a matter of weeks. If the sensor have a power cable it can still have constraints as some sensors still use wireless protocols for transmitting the data and then this will be the limiting constraint. The important part is to see a minimum of ~10 rotations of the equipment each time a sample is taken. This means that the right sample length is dependent on the RPM of your assets. An interval of at least once an hour is a good place to start but we have seem promising results by doing it at a more frequent interval.
Be aware that if you sample often and have a large sample length with a high frequency sensor you will receive largest amounts of data over time. In general it is better to over sample than to under sample as it is easy to delete data or filter it out but it is impossible to invent data which was never collected.
Conclusion
Selecting the right vibration sensor is not trivial and requires you to do some research on your assets RPM and the sensors available. Vibration monitoring running continuously generates a large amount of data no matter what interval and length you select but it is depend on these choices. Due to the size of the data and the minuscule change in vibrations we recommend you use machine learning to figure out the patterns and not do upper and lower control limits as these are likely to miss the changes for a long time. We often call the machine learning approach predictive maintenance and upper and lower control limits for condition-based maintenance. If you want to know more about the difference between condition-based maintenance and predictive maintenance and why upper and lower control limits can give a false sense of security or over alarm we encourage you to read this blog post.
The current sensor market with all the new advancement especially in IoT within vibration monitoring is a jungle and we hope that this blog post have helped you frame what is important to look for when selecting a solution to help you digitize your maintenance.
If you have any questions regarding your next project you are always welcome to contact us it is and always will be free of charge.
// Rasmus Steiniche, CEO @ neurospace