Nordic Sugar i Nakskov har identificeret en optimeringsmulighed, ved at benytte en mere databaseret tilgang til deres krystallisationsapparater. I forbindelse med projektet fik Nordic Sugar og Neurospace lavet en taskforce til, at undersøge muligheden for at bruge maskinlæring til at give databaseret feedback til operatøren og derved bruge mindre energi i produktionen.
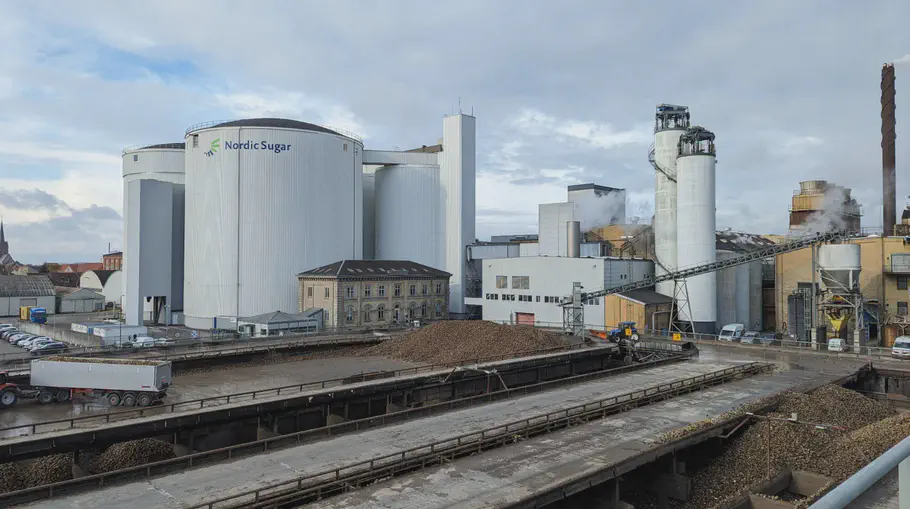
Fakta om virksomheden
Nordic Sugar A/S blev startet tilbage i 1883, og er i dag en del af Nordzucker koncernen. Fabrikken spiller en central rolle i udviklingen af en grønnere dagsorden i sukkerproduktionen i Europa, og har et strategisk mål om at reducere deres udledning med 70% inden 2030.
Opsummering
Grundlæggende viden omkring krystallisationsapparater
Krystallisationsapparater i sukkerproduktion anvendes til at koncentrere sukkeropløsningen ved tryk og temperatur. Vakuumet tillader vandet i sukkeropløsningen at fordampe ved lavere temperaturer, så sukkeret ikke beskadiges. Den resulterende koncentrerede sukkeropløsning gennemgår herefter krystalliseringsprocessen, hvor sukkerkrystaller dannes.
Dampen, som bruges i krystallisationsapparaterne, er genbrugt fra tidligere produktionstrin, hvor der er behov for en højere temperatur på dampen. Derfor dækkes krystallisationsapparaternes energibehov af genanvendt restvarme fra fordampningen (trin 4 og trin 5) på fabrikken. Dampen kan hertil ikke længere bruges, da selve nedkølingen af dampen bruges til at skabe det vakuum, der er indeni apparaterne.
Ved at genbruge dampen fra de forrige processer øges fabrikkens totale energieffektivitet og på denne måde styrker Nordic Sugars mål omkring grønnere produktion af sukker.
Projektet
Nordic Sugars produktion kører 24/7 fra den første roe bliver gravet op til den sidste bliver lavet til sukker. Denne periode beskrives også som en “kampagne”. Produktionen skal ses som et etstrengsanlæg og hver led i produktionen har en takttid som skal overholdes. Når produktionen kører i døgndrift er det essentielt at alle takttider bliver overholdt for at sikre, at der ikke kommer forstyrrelser i produktionen.
Operatørerne i produktionen har fundet et uudnyttet potentiale i, at takttiden omkring krystallisationsapparaterne ofte ikke blev udnyttet fuldt ud. Dette skyldes, at sukkeropløsningen ofte kan koges færdig hurtigere end de 3 timer for A-produkt, som takttiden er på. I praksis betød dette, at der blev brugt for meget af trin 4 dampen (høj energi), og der var et potentiale for at benytte sig af mere trin 5 damp (lav energi) for at udnytte takttiden fuldt ud med en lavere effekt.
Nordic Sugar og Neurospace fik lavet et opstartsmøde, hvor udfordringen blev belyst og der blev primært vidensdelt mod Neurospace for at sikre, at den nødvendige domæneviden var til stede før påbegyndelsen af arbejdet. Der var ikke noget entydigt svar på, hvordan opgaven skulle løses. Det viste sig dog, at det var vigtigt at involvere domæneeksperterne, som i dette tilfælde var operatørerne og relevante driftteknikere. Eksperterne kunne give indsigt i, hvordan produktionen foregik, og hvilke faktorer der var vigtige at tage hensyn til. På baggrund af denne viden og data fra tidligere produktionskampagner, blev der udviklet en maskinlæringsmodel, som kunne forudsige, hvornår det var nødvendigt at skifte fra trin 5 damp til trin 4 damp.
Resultater
Det vi forudså og estimerede på baggrund af pilotprojektet var | ||
---|---|---|
Forøgelse af trin 5 damp | 7% | 43% |
Effektbehov | 6.349 kWh | 39.004 kWh |
Diesel | 634 liter | 3897 liter |
CO2 | 1690 kg | 10.385 kg |
Test kampagnen foregik over 34 dage og ML modellen blev testet på 2 krystalliseringsapparater.
Resultatet fra test kampagnen blev | ||
---|---|---|
Forøgelse af trin 5 damp | 40% | |
Diesel | 3000+ liter |
Dette resultat indeholder et bias, da processen, på nuværende tidspunkt, fungerer med såkaldt ‘Human in the loop’. Dette betyder at en operatør stadigvæk skal ændre setpunktet. Forskellen er nu, at de har et værktøj, de kan bruge til at træffe en bedre og hurtigere beslutning på baggrund af OWLS-modellens forudsigelser.
Konkret har operatørerne indstillet setpunktet i 80 ud af 104 kog, hvor de førhen indstillede setpunktet i 30 ud af 104 i samme periode. Det kan derfor konstateres, at OWLS-modellen har hjulpet operatørerne med at træffe gode beslutninger oftere, hvilket også er det vi ser ved reduceringen i energiforbruget.
Hvis man på sigt fuldautomatiserer modellens styring, af forbruget af effekt 5 damp, vil setpunktet sandsynligvis blive ændret oftere. Dermed vil gevinsten ved at anvende modellen være endnu større, end det vi har set på de 34 dage.
Udover at reducere energiforbruget har projektet også haft en positiv indvirkning på effektiviteten og damp balancen på fabrikken.
OWLS casen skal ses som en dynamisk løsning, da forholdene i et krystalliseringsapparat afhænger af en lang række faktorer såsom apparaternes størrelse, type, rørføring og generelt hvordan fabrikken driftes. Nordic Sugar valgte at samarbejde med Neurospace og satse på en maskinlæringsløsning, fordi de havde en klar forventning til projektets potentiale, og til hvilke faktorer der skulle indgå i en statisk løsning. Samtidig havde de en masse åbne spørgsmål og et klart ønske om en metode som kan genbruges på tværs af apparater og fabrikker.
Skaleringspotentialet
Metoden udviklet under OWLS-projektet, træner nogle meget små ML modeller, som svarer på nogle meget konkrete spørgsmål. Dermed kan metoden benyttes til at træne specialiserede modeller fra bunden på nye krystalliseringsapparater. Det tager i omtrent ét minut at træne og afsøge de optimale hyperparametre, for de modeller der giver ophav til resultaterne beskrevet ovenfor.
I Neurospace forsøger vi at skære problemet helt til benet, hvor vi ingen ambitioner har om at bygge store generelle ML modeller. Dette kalder vi “Lean maskinlæring”. På den måde skaber den lille investering, som Nordic Sugar lagde i projektet, hurtigt stor værdi helt uden at bruge unødig energi på at drive gigantiske modeller.